
Committed to Circularity in Pharmaceutical Blister Packaging
VinylPlus® PharmPack is a collaborative project advancing the circularity of PVC pharmaceutical blister packaging in Europe. By bringing together leading PVC film manufacturers, recyclers, and VinylPlus®, the project aims to develop scalable recycling solutions and improve the sustainability of pharmaceutical packaging.
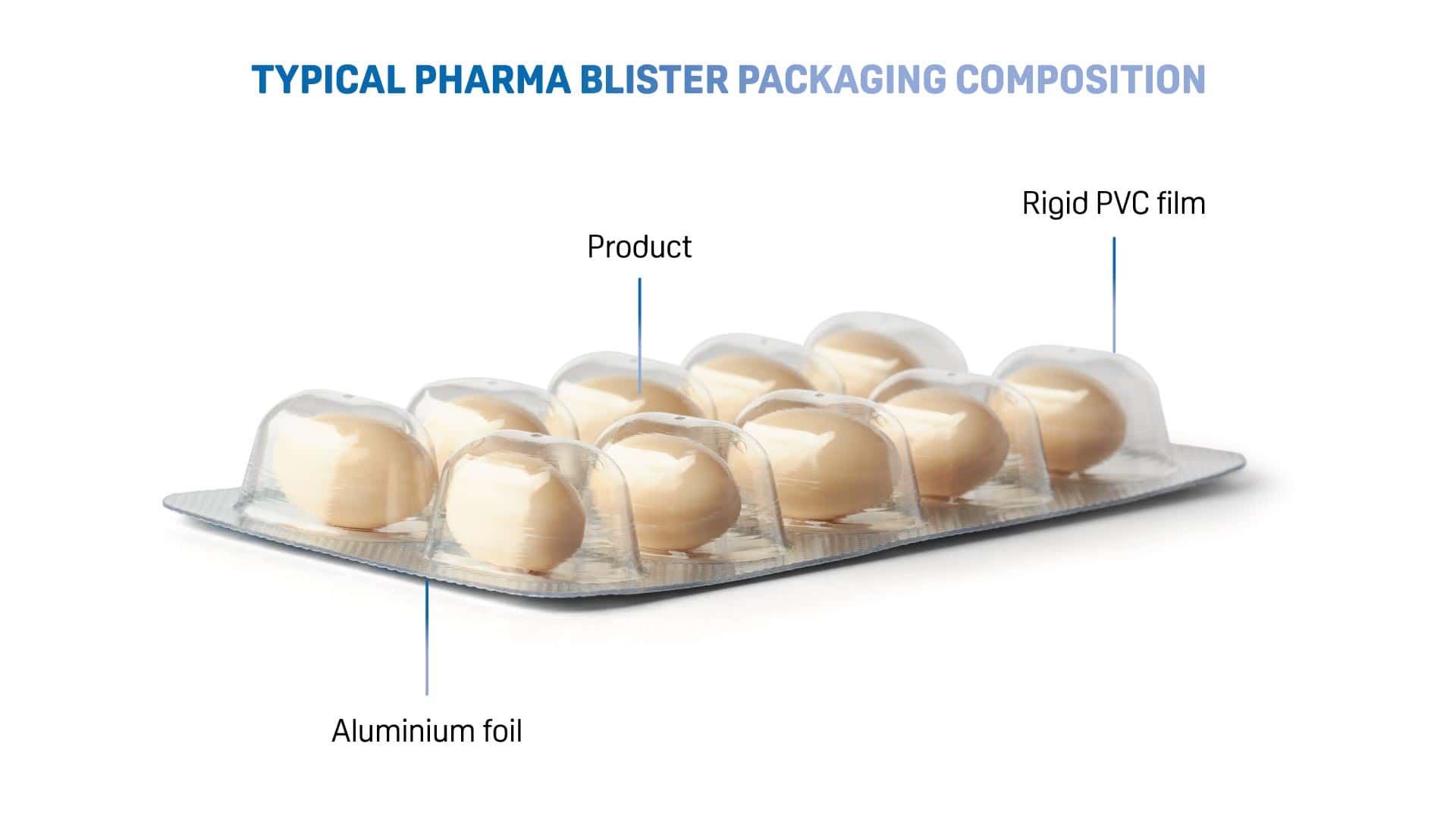
PVC: The Standard Base Material for Pharmaceutical Blister Packaging
In the pharmaceutical industry, packaging is essential for preserving the integrity of medications, ensuring their safe delivery to patients, and extending shelf life. In Europe, blister packaging is widely favoured due to its protective and functional advantages.
Pharmaceutical blister packs are typically made from rigid polyvinyl chloride (PVC or vinyl) films often coated with PVDC and combined with aluminium foil, offering exceptional barrier properties against moisture, oxygen, and contaminants. PVC blisters also provide mechanical strength, protecting medications from physical damage during transport and storage, while allowing for precise, unit-dose dispensing without compromising the remaining product.
Towards a Closed Loop for Rigid PVC Films
Mechanical recycling of pre-consumer PVC blister packaging waste is already well-established in Europe. The VinylPlus PharmPack project aims to enhance the circularity of rigid PVC films used in pharmaceutical packaging by improving recycling pathways. This involves collecting post-consumer waste for established mechanical recycling and demonstrating that high-quality recyclate can be recovered from advanced physical recycling technologies that can be used for new PVC films.
High-Purity Recyclate Through Dissolution
At the heart of this initiative is the CreaSolv® process, an advanced dissolution technology developed by Fraunhofer IVV and CreaCycle GmbH.
Unlike traditional mechanical recycling, where recycled PVC often contains trace amounts of aluminium and vice versa, dissolution technology selectively dissolves PVC, effectively separating it from aluminium and breaking down coatings like PVDC. This results in exceptionally pure PVC recyclate (rPVC). This process has the potential to enable the production of high-quality recycled PVC for new films while ensuring the recovered aluminium meets the stringent quality requirements for many critical applications.
Crucially, unlike chemical recycling, dissolution preserves the polymer structure, making it a physical recycling method that ensures both material integrity and high purity.
Following successful small-scale trials, pilot-scale tests at Fraunhofer IVV have validated the process on a larger scale. Pharma-grade blisters containing 30% rPVC have been successfully produced by Perlen and Liveo Research. This demonstrates that the rPVC produced through the dissolution process is suitable for high-quality applications.
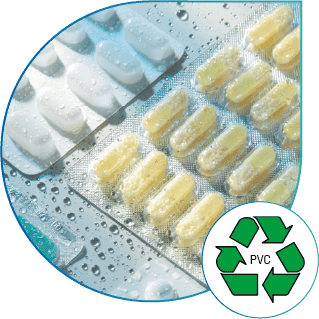
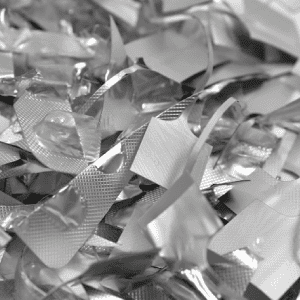
COLLECTION
Punched grids, empty blisters, and materials from film and packaging production are collected and transported to recycling partners.
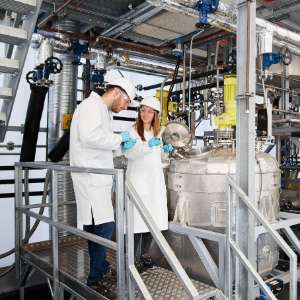
DISSOLUTION
The waste is treated with dissolution technology (photo © Fraunhofer IVV).
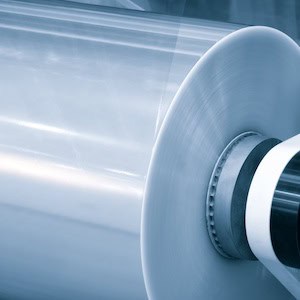
USE OF RECYCLED PVC
The purified rPVC can potentially be used to produce new film.
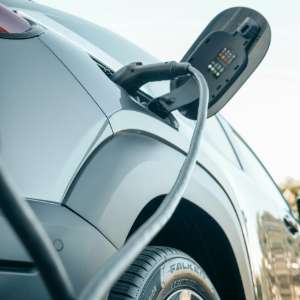
USE OF RECYCLED ALUMINIUM
The purified aluminium can be used for components for electric vehicles and many other critical applications.
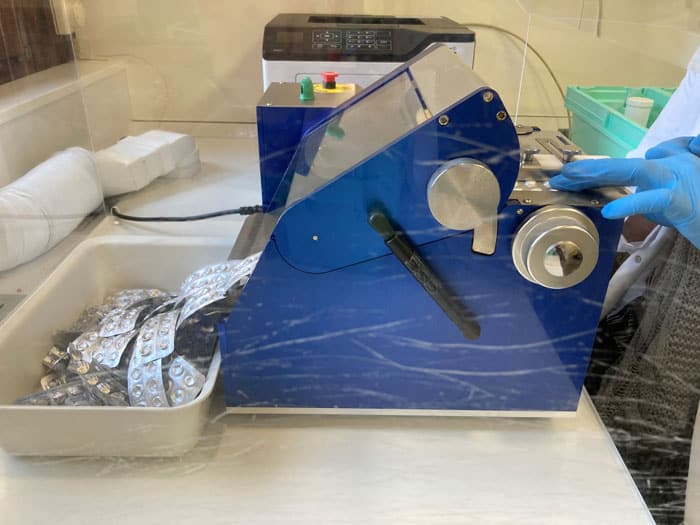
Collection of Post-Consumer Blisters Launched
To complement this technical breakthrough, a pilot collection programme has been launched in German hospital pharmacies, testing the feasibility of systematically recovering post-consumer blister packaging directly from the healthcare sector.
So far, post-consumer PVC-alu blisters are being successfully collected at the hospital pharmacy in Gummersbach, where they are automatically emptied through a unit-dose system before being sent for recycling. The process has proven to be smooth and well integrated into existing workflows, with no significant added burden for staff.
The recovered blisters passed quality checks at the Neidhardt Rohstoff recycling facility and have already been processed alongside pre-consumer waste. The materials are mechanically separated into PVC and aluminium, enabling the production of new items such as spacer profiles for construction and lightweight aluminium parts for the automotive industry.
The insights from this initiative will help define a scalable, circular model for PVC pharmaceutical packaging in Europe.
Our Partners
Expert Insights
Discover more about PVC film producer Perlen Packaging’s involvement in the project and the recycling technologies being tested in the interviews with Dr. Michael Nedelcu, Development Manager:
Current Recycling Practice
While VinylPlus® PharmPack is driving innovation in post-consumer recycling, pre-consumer PVC blister packaging waste has already been successfully recycled in Europe for years. Waste generated during the manufacturing of PVC films, blisters, and pharmaceutical packaging is collected, processed, and separated into PVC and aluminium fractions. These materials are then repurposed in various industries.
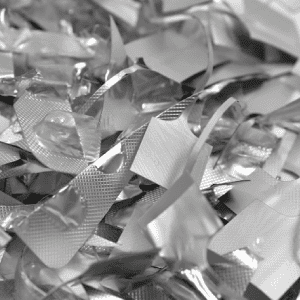
COLLECTION
Punched grids, empty blisters, and materials from film and packaging production are collected and transported to recycling partners.
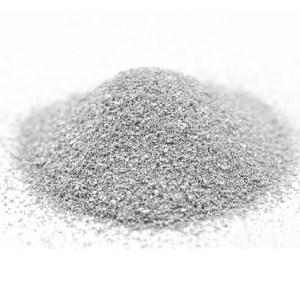
MILLING & SEPARATION
The pre-consumer waste is milled and separated into its main fractions, PVC and aluminium.
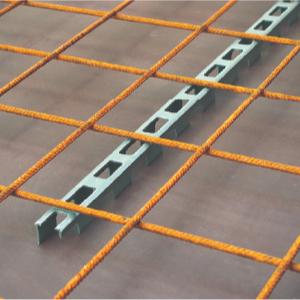
USE OF RECYCLED PVC
The fine PVC regrind is typically used for spacer profiles for the construction industry (image courtesy of MAX FRANK Gruppe).
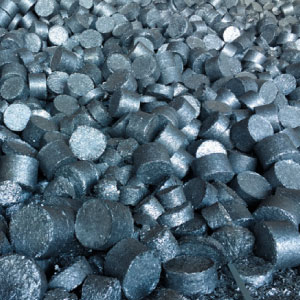
USE OF RECYCLED ALUMINIUM
Aluminium pellets are used in the metal industry such as new engine blocks.